India KVK Thermal Power Plant
Project Overview:
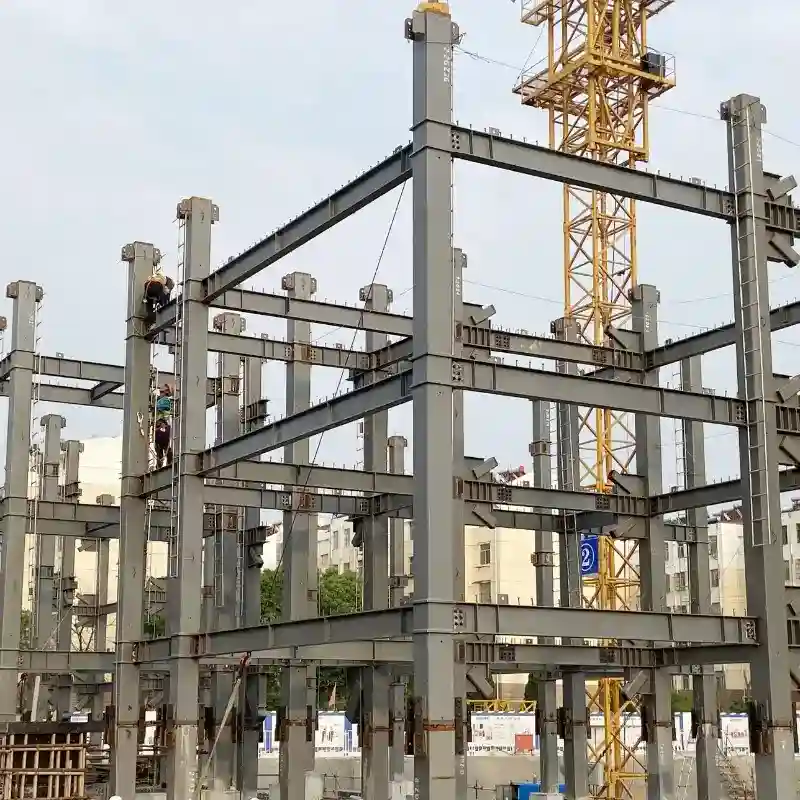
India KVK Thermal Power Plant Phase 1 Unit 1 (1×350MW) BTG Island Project, the construction site is located in Hyderabad, a city in the south of India, designed by China Electric Power Engineering Consultant Group Zhongnan Electric Power Design Institute. The 12th Division of Honglu Group undertook the construction of the main plant, main plant enclosure, flue support, furnace front platform, feeder support, induced draft fan support, steel coal hopper, underfloor recycling facilities and other parts of the project, with a contracted work volume of about 4,600 tonnes.
The main plant of the project consists of three major parts, namely, car room, deoxidising room and coal bunker room, with a span of 9-26m and a length of 89-98m. The structural frame is a transverse stiffened frame + braced structural system, and the longitudinal is an articulated row frame + braced system, which is a typical structure of a thermal power plant plant. Due to the high requirements of electric power equipment on the strength and toughness of steel structure, the 12th Division attaches great importance to the strict control on the procurement of materials, in addition to the requirements of conventional tensile strength, elongation, yield strength, cold bending experiments, but also required to have a room temperature impact toughness and anti-tear Z-direction performance guarantee. In the processing of components, a variety of components for 1:1 sampling. Crane beam flange plate, web length using fixed-foot plate, web in the upper and lower flange plate connection along the length of the planing flat and open cut-outs. Welded steel columns, web splicing position and flange plate splicing position staggered more than 300mm to meet the principle of technology. Pre-assembly requires all node connectors are loaded, in addition to checking the dimensions of each size, but also the use of test hole device to check the plate superimposed on the rate of passage of the holes, the requirement of the perforation rate of 100 per cent.
The most difficult component in the project is the steel coal hopper, the largest of the six coal hoppers weighs more than 60 tonnes, and it is very difficult to turn over, assemble and weld. The group company held an expert meeting with the twelve divisions, and finally determined the split production programme: the cylindrical part of the steel coal hopper was split into three sections of 3000mm, 3000mm and 2050mm wide along the height of the wall plate (8050mm); the circumferential direction was split into a quarter-circle processing and production, and the lengths of the [25a channel and L100*6 angle steel outside the wall of the hopper were divided into a quarter of the circumference minus 1000mm, and then into a quarter length minus 1000mm, and then into a quarter length minus 1000mm. A quarter of the length and then subtract 1000mm, rolled into shape and welded to the wall plate; the height of the conical bucket (3040mm) direction according to the circumferential direction is split into a quarter-circle processing and production, the circumferential diameter of the circle is less than 2782mm are always made according to the whole piece, without splitting; steel coal hopper roof according to the length of the I-beam I16a length of the direction is divided into four pieces, the two grooves 7500 * 600 placed in a piece, the According to the drawings to determine the production. All the holes or holes and slots on the steel coal hopper are cut and welded on site, and all the parts must be preassembled in the workshop for each section of the circumference, and after confirming that they are qualified and error-free, they are marked and numbered.
Due to the high number of transport loading and unloading in this project, in order to prevent damage and deformation of the components, all components except steel columns are framed and packed. The 12th Division will take quality and efficiency as the guide, serve the customers with utmost precision and sincerity, and lay a solid foundation for the company to expand the overseas market.